Tuning a motion control system with ultra-precision controllers like ACS Motion Control or Elmo servo drives requires a systematic approach to ensure optimal performance. Dynamic tests are crucial for assessing system behavior under real-time motion conditions. Here’s an exhaustive list of standard procedures to follow during dynamic tests when tuning these systems:
1- Safety Checks and Setup:
- Verify Safety Limits: Confirm that hardware and software safety limits (e.g., soft and hard stops, torque limits) are correctly configured before testing.
- Emergency Stop Functionality: Ensure emergency stop buttons and limit switches are operational.
- Mechanical Inspection: Check for loose parts, mechanical play, or misalignments in the mechanical structure.
- Power Supply Check: Ensure the servo drives and controllers are receiving stable and correct voltage.
- Encoder Calibration/Alignment: Verify that encoders are properly aligned and calibrated to ensure accurate feedback.
2. Initial System Identification:
- Motor Data Verification: Cross-check motor specifications (e.g., torque constant, resistance, inductance) with system settings.
- Load Characterization: Measure or estimate the system’s load inertia, stiffness, and friction. Compare with motor and drive capability.
- Basic Signal Testing: Perform simple motion commands to verify that basic motion is possible without issues.
- Zeroing/Homing Procedures: Run homing sequences to establish a repeatable reference position for the system.
3. Basic Tuning Procedures:
- Control Loop Type Setup:
- Ensure correct control loop configuration (e.g., current/velocity/position loops).
- Manual PID Tuning:
- Start by tuning the current loop (if applicable), then proceed to the velocity and position loops.
- Use conservative gains to avoid instability in the initial tests.
- Proportional Gain (P): Adjust to minimize position/velocity error.
- Integral Gain (I): Fine-tune to remove steady-state errors.
- Derivative Gain (D): Use to dampen oscillations, but avoid excessive derivative action.
4. Dynamic Performance Tests:
- Open Loop Tests (if applicable):
- Run open-loop tests to ensure motor and drive functionality without feedback influence.
- Measure the response time and motor behavior (current, velocity).
- Step Response Tests:
- Perform step input tests to observe system response in terms of rise time, overshoot, and settling time.
- Capture position/velocity response during acceleration and deceleration.
- Bode Plot Analysis (Frequency Response Test):
- Generate Bode plots to identify resonance frequencies, bandwidth, and phase margins.
- Analyze system stability and adjust filters or PID gains based on frequency response data.
- Sinusoidal Sweep Testing:
- Apply sinusoidal reference signals at various frequencies and amplitudes to verify system tracking performance.
- Impulse/Disturbance Rejection Test:
- Apply external disturbances (torque or load) to evaluate how quickly the system compensates and stabilizes.
- Tune feedforward gains or implement filters if necessary.
5. Error Analysis and Feedforward Tuning:
- Position Error (Following Error):
- Record position following errors and determine if gains or system mechanics need adjustments.
- Fine-tune feedforward control to reduce following error during rapid acceleration/deceleration.
- Velocity Error:
- Check velocity loop performance and refine velocity feedforward terms.
- Evaluate velocity ripple and correct using filters or improved velocity loop tuning.
- Current Loop Error: (if applicable)
- Monitor motor current and compare with the command signal to ensure accurate current control.
6. Advanced Compensation Techniques:
- Notch Filter Tuning:
- Implement and tune notch filters to suppress mechanical resonance frequencies identified during dynamic tests.
- Low-Pass Filter Tuning:
- Use low-pass filters to eliminate high-frequency noise from feedback sensors.
- Advanced Gain Scheduling:
- Adjust control loop gains dynamically based on system state (position, velocity, load changes).
- Adaptive Control:
- If supported, enable and fine-tune adaptive control algorithms to adjust tuning parameters in real time.
- Friction and Cogging Compensation:
- Apply friction compensation and cogging torque compensation based on the system’s friction model.
7. Trajectory and Profile Testing:
- Standard Motion Profiles:
- Test standard motion profiles such as trapezoidal, S-curve, or custom velocity profiles.
- Evaluate system behavior during acceleration, constant velocity, and deceleration.
- Path Following and Contouring Accuracy:
- Test multi-axis coordinated motion (if applicable) for path following and contour accuracy.
- Check and correct for motion profile distortions caused by dynamics.
- High-Speed Testing:
- Evaluate system performance at high speeds, verifying motor and drive behavior under these conditions.
- Stop and Hold Testing:
- Perform abrupt stop tests to evaluate the system’s braking and hold performance (especially for vertical axes or critical applications).
8. Thermal and Electrical Considerations:
- Drive and Motor Temperature Monitoring:
- Monitor motor and servo drive temperatures during tests to avoid overheating.
- Validate that temperature protection mechanisms are functioning properly.
- Power Consumption and Current Monitoring:
- Measure power consumption, current spikes, and overall system power efficiency under dynamic conditions.
- Back EMF Compensation:
- Tune back EMF compensation (if supported) for better performance at high speeds or during dynamic braking.
9. Logging and Data Analysis:
- Capture Data Logs:
- Use the motion controller’s built-in logging tools to record detailed data (e.g., encoder feedback, current, position, and velocity errors) during tests.
- Log both transient (startup, stop) and steady-state conditions.
- Performance Metrics Analysis:
- Analyze performance metrics such as rise time, overshoot, damping, steady-state error, and position accuracy.
- Error and Alarm Analysis:
- Identify and troubleshoot any system errors or alarms generated during dynamic testing.
- Frequency and Time-Domain Data Analysis:
- Analyze system behavior both in the frequency domain (using tools like FFT) and time domain for a comprehensive understanding of performance.
10. System Finalization:
- Closed-Loop Stability Check:
- Perform a final system stability test under varying conditions (load, speed, temperature) to confirm reliable closed-loop behavior.
- Long-Term Drift Testing:
- Run prolonged tests to monitor for position or velocity drift over time.
- Operational Range Testing:
- Test the system under its full operational range (minimum to maximum load, velocity, and acceleration) to ensure robustness.
- Backup and Documentation:
- Save and backup all tuning parameters, including gains, filters, and any compensations applied.
- Document the tuning process, test results, and any special conditions observed.
11. Final Validation and Application Testing:
- Load Testing Under Real-World Conditions:
- Test the system with actual loads, speeds, and conditions relevant to its application.
- Repetition and Repeatability Testing:
- Perform repeated motion cycles to verify long-term repeatability and consistency in motion performance.
- Multi-Axis Synchronization (if applicable):
- Verify coordinated motion across multiple axes, ensuring that synchronization is within acceptable limits.
- Final Accuracy Validation:
- Test system accuracy by comparing actual versus commanded motion profiles over a series of movements.
Conclusion:
By following these standard procedures during dynamic tests, you ensure that ultra-precision motion systems are properly tuned for optimal performance, reliability, and safety. Each step helps identify issues, correct deviations, and fine-tune the system for high-performance applications.
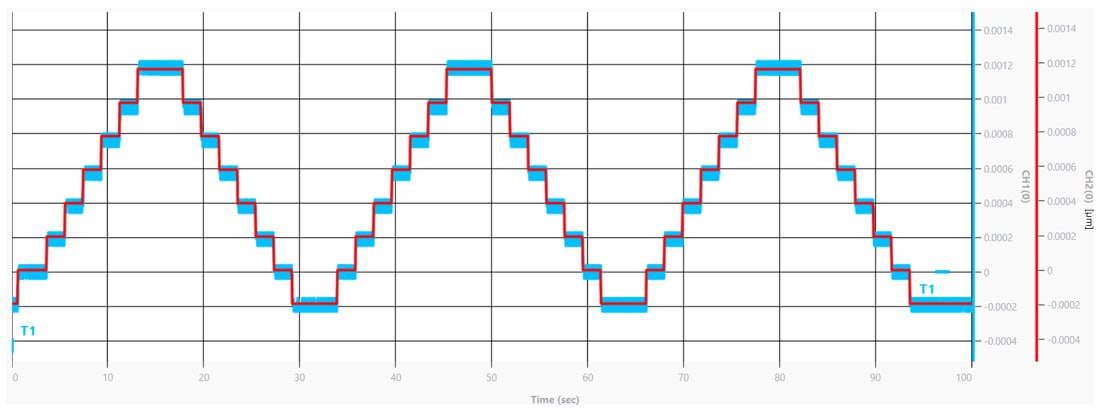